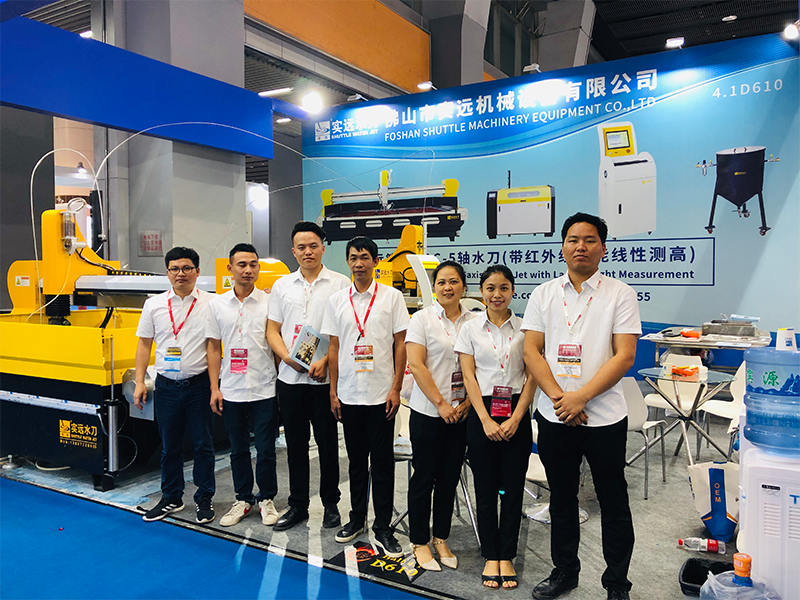
How to effectively maintain the waterjet cutting machine?
First. Daily maintenance
Relevant personnel must clean the equipment every day after finishing processing to keep the machine tool and guide rail clean; pay attention to whether the power and air source are turned off; if there is residual air in the pipe belt of the cutting machine, empty it; if If the machine is not used for a long time, turn off the power in time; also pay attention to whether the lubrication of the horizontal and vertical guide rails and rack surfaces is good.
Second. Weekly maintenance
If the horizontal and vertical rail wipers of the waterjet cutting machine are abnormal, they must be replaced with new ones in time. Loose cutting torches, garbage on the firing muzzle, and automatic height adjustment devices are all areas that require special attention.
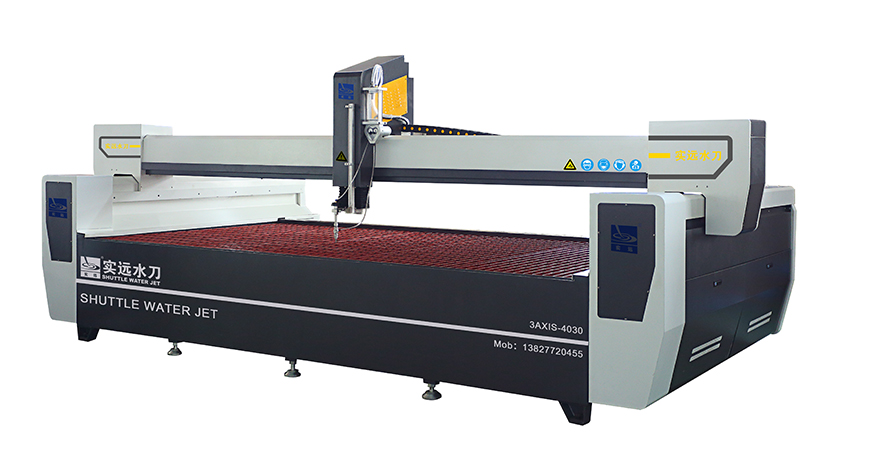
Third. Monthly maintenance
Make a summary of the daily and weekly maintenance work of the waterjet cutting machine, and conduct a complete inspection of the entire equipment, not letting go of every part.
1. Familiar with the water jet from the nozzle of the waterjet cutting machine. Turn on the water flow at low pressure and observe. The water flow should be symmetrical and its width depends on the type of nozzle used. The flow of ruby and sapphire nozzles is slightly wider; the flow of diamond nozzles is narrower and more continuous. If the water flow starts to widen, it means that the nozzle is damaged and should be replaced immediately. A damaged nozzle (or misplaced pipe) will cause internal damage to the cutting head.
2. Regularly check the cutting head for signs of wear or damage (often caused by accidental contact with parts or fixtures). For example, accidental contact of the mixing tube with the clamp can damage the nozzle nut and internal parts that keep the mixing tube aligned.
3. Check the system and keep it in good working condition, so as to make the waterjet cutting operation more effective and extend the service life of its parts. Regularly inspect and replace consumable parts of the sand conveying system, such as pipes and joints. Ensure that no parts of the sand conveying system below the bottom of the micro hopper are exposed to air. When testing this, disconnect the sand conveying pipeline from the joint at the bottom of the micro hopper, manually turn on the jet and stick your thumb to one end of the sand conveying pipeline. You will feel ample (but not excessive) vacuum, which may dent the tip of your thumb. Insufficient vacuum may indicate that the entrance of the cutting head is blocked, or there are cracks in the sand conveying pipeline, which must be resolved at this time to fully utilize the efficiency of the system.
Relevant personnel must clean the equipment every day after finishing processing to keep the machine tool and guide rail clean; pay attention to whether the power and air source are turned off; if there is residual air in the pipe belt of the cutting machine, empty it; if If the machine is not used for a long time, turn off the power in time; also pay attention to whether the lubrication of the horizontal and vertical guide rails and rack surfaces is good.
Second. Weekly maintenance
If the horizontal and vertical rail wipers of the waterjet cutting machine are abnormal, they must be replaced with new ones in time. Loose cutting torches, garbage on the firing muzzle, and automatic height adjustment devices are all areas that require special attention.
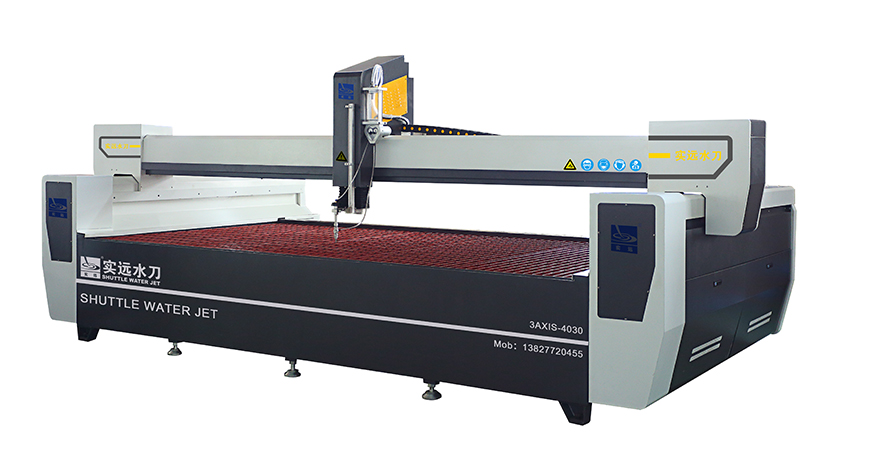
Third. Monthly maintenance
Make a summary of the daily and weekly maintenance work of the waterjet cutting machine, and conduct a complete inspection of the entire equipment, not letting go of every part.
1. Familiar with the water jet from the nozzle of the waterjet cutting machine. Turn on the water flow at low pressure and observe. The water flow should be symmetrical and its width depends on the type of nozzle used. The flow of ruby and sapphire nozzles is slightly wider; the flow of diamond nozzles is narrower and more continuous. If the water flow starts to widen, it means that the nozzle is damaged and should be replaced immediately. A damaged nozzle (or misplaced pipe) will cause internal damage to the cutting head.
2. Regularly check the cutting head for signs of wear or damage (often caused by accidental contact with parts or fixtures). For example, accidental contact of the mixing tube with the clamp can damage the nozzle nut and internal parts that keep the mixing tube aligned.
3. Check the system and keep it in good working condition, so as to make the waterjet cutting operation more effective and extend the service life of its parts. Regularly inspect and replace consumable parts of the sand conveying system, such as pipes and joints. Ensure that no parts of the sand conveying system below the bottom of the micro hopper are exposed to air. When testing this, disconnect the sand conveying pipeline from the joint at the bottom of the micro hopper, manually turn on the jet and stick your thumb to one end of the sand conveying pipeline. You will feel ample (but not excessive) vacuum, which may dent the tip of your thumb. Insufficient vacuum may indicate that the entrance of the cutting head is blocked, or there are cracks in the sand conveying pipeline, which must be resolved at this time to fully utilize the efficiency of the system.